Ranskan aurinkoenergiainstituutti INES on kehittänyt uusia PV -moduuleja, joissa on Euroopassa hankitut kestomuovit ja luonnolliset kuidut, kuten pellava ja basaltti. Tutkijoiden tavoitteena on vähentää aurinkopaneelien ympäristöjalanjälkeä ja painoa parantaen samalla kierrätystä.
Kierrätetty lasipaneeli edessä ja liinavaatekomposiitti takana
Kuva: GD
PV -lehdestä France
Ranskan kansallisen aurinkoenergiainstituutin (INES) tutkijat-ranskalaisten vaihtoehtoisten energioiden ja atomienergiakomission (CEA) osasto-kehittävät aurinkosamoduuleja, joissa on uusia biopohjaisia materiaaleja etu- ja takapuolilla.
"Koska hiilijalanjäljestä ja elinkaarianalyysistä on nyt tullut välttämättömiä kriteerejä aurinkosähköpaneelien valinnassa, materiaalien hankinta tulee tärkeä osa Euroopassa seuraavien vuosien aikana", sanoi CEA-iansin johtaja Anis Fouini, CEA , PV -lehden France -lehden haastattelussa.
Tutkimusprojektin koordinaattori Aude Derrier kertoi, että hänen kollegansa ovat tarkastelleet jo olemassa olevia materiaaleja löytääkseen sellaisen, jonka avulla moduulien valmistajat voivat tuottaa paneeleja, jotka parantavat suorituskykyä, kestävyyttä ja kustannuksia, samalla kun vähentävät ympäristövaikutuksia. Ensimmäinen mielenosoittaja koostuu heterojunction (HTJ) aurinkokennoista, jotka on integroitu koko komposiittimateriaaliin.
"Etupuoli on valmistettu lasikuitua täytetystä polymeeristä, joka tarjoaa läpinäkyvyyden", Derrier sanoi. "Takaosa on valmistettu komposiitista, joka perustuu kestomuovisiin, joissa kahden kuidun, pellavan ja basaltin kutominen on integroitu, mikä tarjoaa mekaanisen lujuuden, mutta myös paremman kosteudenkestävyyden."
Pellava on peräisin Pohjois -Ranskasta, missä koko teollisuusekosysteemi on jo läsnä. Basaltti on peräisin muualle Euroopasta, ja INES: n teollisuuskumppani on kudottu. Tämä vähensi hiilijalanjälkeä 75 grammalla hiilidioksidia wattia kohti verrattuna saman tehon vertailumoduuliin. Paino myös optimoitiin ja se on alle 5 kiloa neliömetriä kohti.
"Tämä moduuli on suunnattu katolle PV ja rakennusten integrointiin", Derrier sanoi. ”Etuna on, että se on luonnollisesti musta väriltään ilman takulautanen tarvetta. Kierrätyksen kannalta kestomuovien ansiosta, joka voidaan uudistaa, kerrosten erottaminen on myös teknisesti yksinkertaisempaa. "
Moduuli voidaan valmistaa mukauttamatta nykyisiä prosesseja. Derrier sanoi, että ajatuksena on siirtää tekniikka valmistajille ilman lisäinvestointeja.
"Ainoa välttämätöntä on saada pakastimet materiaalin säilyttämiseksi eikä hartsin silloitusprosessin aloittamiseksi, mutta suurin osa valmistajista käyttää nykyään prepreg ja on jo varustettu tähän", hän sanoi.
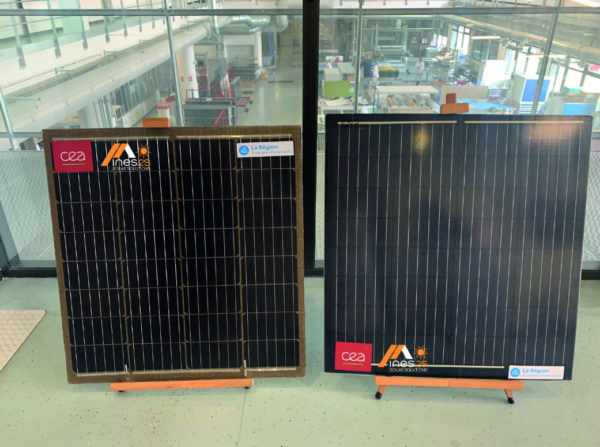
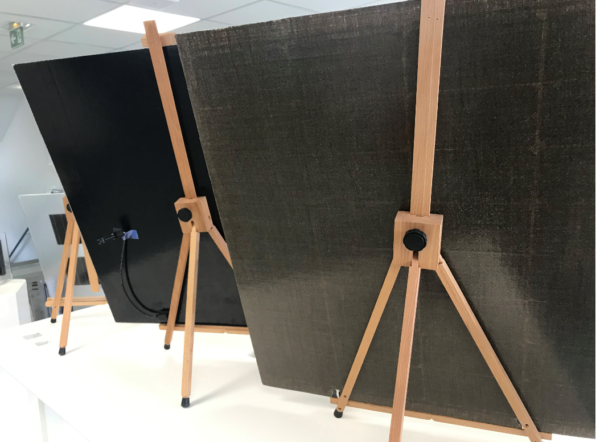
"Työskentelimme lasin toisessa elämässä ja kehitimme moduulin, joka koostuu uudelleenkäytetystä 2,8 mm: n lasista, joka tulee vanhasta moduulista", sanoi Derrier. "Olemme käyttäneet myös kestomuovisia kapselantteja, jotka eivät vaadi silloittumista, joka on siksi helppo kierrättää, ja kestomuovinen komposiitti, jolla on pellavakuitu vastus."
Moduulin basalttivapaassa takapinnassa on luonnollinen liinavaatteiden väri, joka voi olla esteettisesti mielenkiintoinen arkkitehdille esimerkiksi julkisivun integraation suhteen. Lisäksi INES -laskentatyökalu osoitti hiilijalanjäljen vähenemisen 10%.
"Nyt on välttämätöntä kyseenalaistaa aurinkosähköketjut", Jouini sanoi. ”Rhône-Alpes-alueen avulla kansainvälisen kehityssuunnitelman puitteissa etsimme siksi aurinko-alan ulkopuolisia pelaajia etsimään uusia kestomuovia ja uusia kuituja. Ajattelimme myös nykyistä laminointiprosessia, joka on erittäin energiaa intensiivistä. ”
Painetuksen, puristus- ja jäähdytysvaiheen välillä laminointi kestää yleensä 30–35 minuuttia, käyttölämpötila on noin 150 ° C - 160 C.
"Mutta moduuleissa, jotka sisältävät yhä enemmän ekologisia materiaaleja, on välttämätöntä muuttaa lämpömuotot noin 200 ° C: sta 250 ° C: seen tietäen, että HTJ-tekniikka on herkkä lämmölle eikä sen saa ylittää 200 ° C", Derrier sanoi.
Tutkimusinstituutti on yhteistyössä Ranskassa sijaitsevan induktiotermocompression-asiantuntijan Roctoolin kanssa sykli-aikojen vähentämiseksi ja muotojen tekemiseksi asiakkaiden tarpeiden mukaan. Yhdessä he ovat kehittäneet moduulin, jonka takapinta on valmistettu polypropeenityyppisestä kestomuovikomposiitista, joihin kierrätetyt hiilikuidut on integroitu. Etupuoli on valmistettu kestomuoveista ja lasikuituista.
"Roctoolin induktiotermokompressioprosessi mahdollistaa kahden etu- ja takalevyn lämmittämisen nopeasti, joutumatta saavuttamaan 200 ° C HTJ -solujen ytimessä", Derrier sanoi.
Yhtiö väittää, että sijoitus on alhaisempi ja prosessi voisi saavuttaa vain muutaman minuutin sykli -ajan, samalla kun se käyttää vähemmän energiaa. Teknologia on tarkoitettu komposiittivalmistajille, jotta heille annetaan mahdollisuus tuottaa eri muotoja ja kokoja osia integroimalla kevyemmät ja kestävät materiaalit.
Viestin aika: kesäkuu-24-2022